- May 14, 2025
- Posted by: wellcoindustries
- Category: Rebar
Introduction
Steel has been the go‑to reinforcing material for decades, yet every project manager knows the headache that comes with corrosion, spalling, and unexpected maintenance bills. Composite rebar—manufactured from continuous fibers embedded in a tough resin matrix—has surged from niche product to mainstream solution because it tackles those hidden costs head‑on. As a vertically integrated supplier of Fiber Reinforced Plastics (FRP), Wellco Industries draws on global manufacturing and in‑house testing to help contractors, distributors, and OEM customers pivot smoothly toward this next‑generation reinforcement.
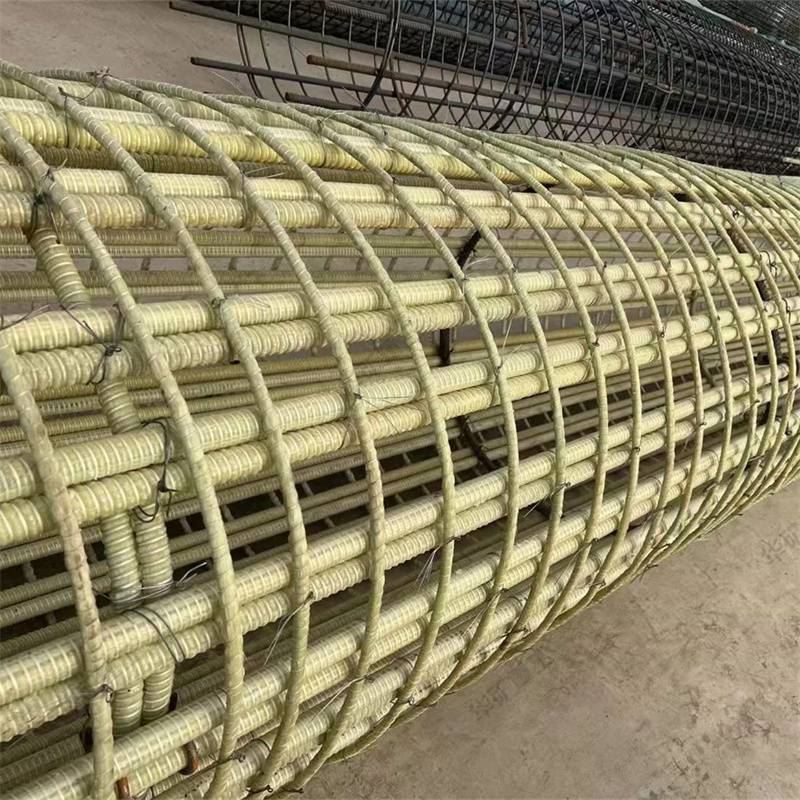
What Is Composite Rebar and How Is It Made?
Core Materials: Fiberglass, Basalt & Resin Matrix
Most composite rebar is built from E‑glass or basalt fibers bundled into strands that offer tensile strengths of 1,000 MPa or higher—roughly double that of Grade 60 steel. A vinyl‑ester or epoxy resin binds those strands, locking in durability while resisting alkaline concrete environments.
Pultrusion & Winding Processes Explained
During pultrusion, fiber tows are pulled through a resin bath, shaped in a heated die, and cured under tension to maintain straightness. Helical surface windings or sand coatings are added for mechanical bond with concrete. The process is highly automated, which allows for consistent quality across long production runs—critical when your spec calls for repeatable performance.
Why Contractors Are Making the Switch
Corrosion Resistance & 100‑Year Service Life
The National Association of Corrosion Engineers (NACE) pegs global infrastructure corrosion losses at 3–4 % of GDP annually—a staggering figure composite rebar directly addresses. Laboratory immersion tests demonstrate negligible strength loss after 100 years of simulated exposure, making it ideal for coastal, de‑icing salt, and wastewater sites.
Up to 75 % Weight Reduction for Easier Handling
“Two workers unloaded an entire pallet with no machinery in under ten minutes,” reports a crew foreman on a municipal seawall rebuild. At roughly one‑quarter the density of steel, composite bars cut crane time and reduce job‑site injuries while slashing freight costs.
High Tensile Strength & Design Flexibility
Because composite bars don’t yield like steel, engineers can design for higher allowable stresses, sometimes trimming bar counts. Their non‑magnetic and non‑conductive nature also eliminates stray current issues around MRI rooms, utility vaults, and rail systems.
Real‑World Applications & Case Study Insights
Bridge Deck Retrofit Saves 25 % Lifecycle Cost
An anonymized Midwestern state DOT specified glass‑fiber composite rebar in a 1960s concrete bridge deck replacement. Finite‑element modeling predicted a 60‑year maintenance‑free span, versus a 20‑year resurfacing cycle with epoxy‑coated steel. Result: 25 % lower total lifecycle cost even after accounting for a modest upfront premium.
Agricultural Water‑Control Structures Using FRP Grids
Irrigation districts across the U.S. Sun Belt are replacing steel grating with composite reinforcement in low‑head weirs and sluice gates. Corrosion immunity eliminates the need for cathodic protection while allowing gates to stay operational during fertilizer flushes—crucial for growers under tight planting windows.
Specifying & Sourcing Composite Rebar
Relevant ASTM/ACI Standards & Design Codes
-
ASTM D7957: Standard specification for solid round glass‑fiber bars.
-
ACI 440.1R‑24: Design guide with equations for flexure, shear, and serviceability.
-
CSA S807 (Canada) and JSCE guidelines (Japan) provide additional regional criteria.
How Purchasing Managers Vet Suppliers (Wellco Checklist)
-
Third‑party testing certificates for tensile, bond, and creep rupture.
-
ISO 9001 process audits to ensure traceability.
-
Dimensional consistency across multiple lots—critical for automated rebar benders.
-
Technical support: Wellco Industries offers in‑house civil engineers to review drawings, plus job‑site training videos to accelerate crew adoption.
Logistics, MOQ & Private‑Label Options
Composite bars ship in coils or straight lengths. Wellco can bundle mixed diameters in a single container to meet minimum‑order quantities as low as 5 tons. Private‑label color coding, bar‑mark embossing, and bar‑code tracking are available for distributors building their own brand lines.
Conclusion
Composite rebar delivers corrosion immunity, weight savings, and robust tensile performance that steel can’t match. Early adopters are already banking double‑digit lifecycle savings while boosting crew productivity. Ready to future‑proof your next project? Contact Wellco Industries for design assistance, samples, or a turnkey quote from our global FRP manufacturing network.
Frequently Asked Questions
Q1. How does composite rebar bond to concrete without ribs?
Composite bars gain pull‑out strength from sand coatings or helically wound fibers that create a rough surface texture, achieving bond values comparable to deformed steel bars.
Q2. Can I bend composite rebar on site?
Cold bending is not recommended; order factory‑shaped stirrups or use threaded anchors. Heated bending alters resin properties and should follow manufacturer guidelines.
Q3. Is composite rebar approved by major building codes?
Yes. ACI 440 documents and ASTM D7957 are referenced by many state DOTs and international building codes; always confirm local jurisdiction acceptance.
Q4. What temperature limits apply?
Most vinyl‑ester bars handle sustained service up to 180 °F (82 °C). Higher‑temperature epoxy systems are available for industrial furnaces or hot‑mix asphalt contact zones.
Q5. How do lead times compare to steel?
Standard diameters (< 25 mm) ship in 4–6 weeks. Custom colors or larger diameters may require 8 weeks; Wellco’s vertically integrated lines help compress schedules during peak season.