- May 15, 2025
- Posted by: wellcoindustries
- Category: FRP handrails
Introduction
Pressure to trim maintenance budgets while boosting safety has never been higher—especially for construction, agricultural, and infrastructure projects exposed to weather and chemicals every day. Choosing the right guardrail matters more than ever. This article compares fiberglass handrail systems vs. metal handrails on the two factors buyers care about most: cost and durability. Based on field data gathered while supporting Wellco Industries’ global FRP projects, you’ll see how life‑cycle numbers, real‑world corrosion tests, and installer feedback stack up—so you can justify the smartest investment.
“After five years in fertilizer dust and coastal salt spray, our FRP rails still look brand‑new—steel lasted barely two,” — Maintenance Lead, anonymous port grain terminal.
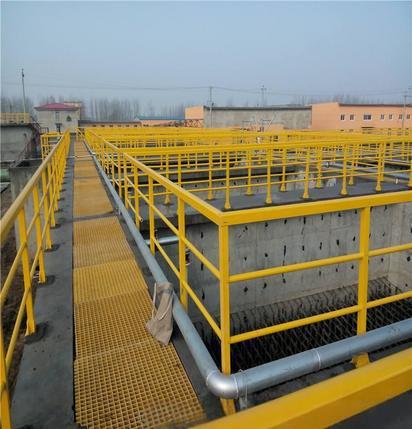
Material Fundamentals – What Are You Really Buying?
Fiberglass Handrail Systems: Pultruded FRP Profiles, Resin Types & Glass Content
Fiberglass rails are pultruded composites: continuous strands of E‑glass saturated with polyester or vinyl‑ester resin, then cured into I‑beams, round tubes, and molded fittings. Mechanical strength comes from glass content (55–70 % by weight) while resin chemistry handles UV, chemicals, and heat. Pigment is cast through the wall, so scratches don’t expose bare substrate.
Metal Handrails: Carbon‑Steel, Stainless, Aluminum—Typical Grades & Coatings
Carbon‑steel rails (A36, A500) rely on galvanizing and periodic paint; stainless (304/316) costs up to 4× more but resists corrosion in most indoor settings; aluminum (6061, 6063) delivers light weight yet sacrifices strength at welds. Every metal choice ultimately depends on a surface coating—once it fails, rust or pitting begins.
Cost Over the Asset Lifecycle
Up‑Front Material & Installation Pricing (per linear foot benchmarks)
Handrail Type | Purchase Price | Typical Install Crew | Avg. Hours / 100 ft |
---|---|---|---|
Carbon Steel, painted | $28–35 | 3 ironworkers | 22 h |
Stainless 304 | $80–95 | 3 ironworkers | 20 h |
Fiberglass (pultruded) | $45–55 | 2 general laborers | 12 h |
Fiberglass starts above carbon steel on material but saves roughly 40 % on labor thanks to light weight (≤ 2 lb/ft) and no hot‑work permits.
Maintenance, Painting & Corrosion‑Repair Expenses (5‑, 10‑, 20‑year view)
-
Carbon steel: repaint every 3–5 yrs ($12–15 / ft each cycle).
-
Stainless: minimal paint, but tea‑staining in coastal zones → passivation ($4–6 / ft each 7 yrs).
-
Fiberglass: rinse & inspection only (< $1 / ft per decade).
ROI Snapshot: anonymized grain‑terminal case study showing 37 % cost savings with FRP
A coastal grain elevator replaced 1,200 ft of corroded steel rails with fiberglass. Over 20 yrs:
-
Steel (status quo) projected cost: $183 k (purchase + 3 paint cycles + rust repairs).
-
FRP actual cost: $115 k (purchase + rinse).
Savings: 37 %, payback in 4.1 yrs—validating Wellco Industries’ total‑cost model.
Durability & Environmental Resistance
Corrosion & Chemical Exposure: ASTM B117 Salt‑Fog Data + Real‑World Farm Quote
ASTM salt‑fog tests show fiberglass strength retention > 95 % after 3,000 hrs, vs. epoxy‑coated steel at 78 %. A farm co‑op using liquid ammonium nitrate reports “zero blistering on FRP rails after two seasons—our galvanized catwalk rail flaked in eight months.”
Structural Strength, Impact & Fatigue: Load Ratings vs. OSHA 1910.29(b)
Pultruded 2‑in. FRP top rails carry 200 lb perpendicular load with 2× safety—matching OSHA guardrail rules. Aluminum meets the same code but deforms sooner under cyclic forklift impacts; mild steel excels in pure impact but rust makes wall thickness an uncertainty.
UV & Temperature Cycling: Comparative Aging Tests, Warranty Implications
-
FRP with UV inhibitors: < 5 % color fade at 10 yrs (Arizona exposure panels).
-
Aluminum chalks; powder coat warranties rarely exceed 5 yrs.
-
Manufacturers like Wellco back FRP rails with 25‑year structural warranties—outlasting most capital budgets.
Safety, Compliance & Worker Experience
Slip Resistance & Thermal Comfort—Why FRP Stays Grippable in Rain or Sun
The molded‑in grit surface scores 0.9 COF (wet) vs. painted steel’s 0.4. Fiberglass also insulates, staying < 10 °C above ambient even under direct sun, preventing “hot‑rail burns” common on black steel.
Regulatory Checklist: OSHA, IBC, Local Codes—Where Metals Still Excel or Fall Short
Both materials pass OSHA guardrail criteria. Stainless often wins fire‑code exemptions in petrochemical zones (> 760 °C tolerance). FRP’s Class 1 flame‑spread rating (ASTM E84 ≤ 25) is accepted in most jurisdictions, but verify local amendments.
Voice of the Field: Short Quote from Site Supervisor on Reduced Injuries After FRP Install
“Hand‑slips dropped to zero last winter—nobody’s grabbing an icy steel pipe anymore,” says the safety supervisor at a Midwest processing plant that swapped 400 ft of mezzanine railing to FRP.
Installation Speed & Customization Options
Modular, Lightweight Components—Labor‑Hour Comparison Table
Two workers with battery saws and wrenches install FRP at roughly 8 ft/hr; steel averages 4 ft/hr due to welding and touch‑up paint. No crane picks or flame‑cutting means fewer permits and faster shutdowns.
Color‑Matching, OEM Branding & Private Label Programs (Leveraging Wellco Industries’ Turnkey Capability)
Because pigment is integral, rails can match safety yellow, green, or a customer’s brand PMS code. For OEMs and private‑label distributors, Wellco Industries supplies cartons marked with custom logos, reducing repackaging steps.
When Metal Remains the Better Fit
High‑Heat Process Areas (> 200 °C)
Close to furnaces or exhaust ducts, resin softening makes FRP unsuitable; stainless or painted carbon steel still rule.
Short‑Term or Budget‑Capped Projects—Risk‑Reward Matrix
If the facility will be demolished or sold within five years, the lower upfront cost of painted steel may trump long‑term savings. A simple matrix weighing project horizon vs. environmental severity clarifies the call.
Conclusion
Fiberglass handrail systems cost more on day one yet repay the difference by slashing installation hours and eliminating decades of repainting. They outperform metals in corrosive, wet, or cold environments, improve worker grip, and carry lengthy structural warranties. Metals retain an edge in extreme‑heat zones or tight‑budget quick fixes. Evaluate service life, exposure, and labor rates—then request Wellco Industries’ engineering data sheets or a rapid quote to see the numbers for your project.
Frequently Asked Questions
Q1. How long do fiberglass handrail systems last in outdoor environments?
Lab UV tests and 20‑year field records show minimal strength loss; expect 25+ years with basic washdowns.
Q2. Can FRP rails be customized to match corporate colors?
Yes. Pigment is added during pultrusion, so any safety yellow or brand color can be matched without later painting.
Q3. Are FRP rails difficult to cut or drill on‑site?
No. Standard carbide blades and bits work; crews wear dust masks, but no special welding or hot‑work permits are needed.
Q4. How does shipping cost compare to metal?
Fiberglass weighs about one‑third of steel, so freight may run 20–40 % less per linear foot, depending on distance.
Q5. What certifications should buyers look for?
Check for ASTM E84 flame‑spread, OSHA 1910.29 load testing, and manufacturer ISO 9001 quality management.